What to know
Mining has one of the highest fatal injury rates of any U.S. industry. Ground falls cause the highest percentage of mining fatalities and injuries. Underground coal reserves are mined under deeper cover, potentially interacting with previous workings. Research on a wide range of geologic factors has helped decrease the number of ground fall injuries and fatalities.
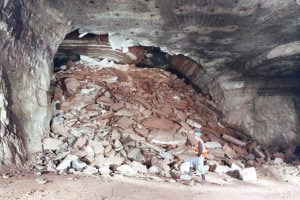
Overview
Ground falls in the mining industry include one of the highest fatal injury rates of any U.S. industry. Between 1999 and 2008, roof, rib, and face falls caused nearly 40% of all underground fatalities. Small pieces of rock falling between bolts injure 400–500 coal mine workers each year.
Additionally, slope failure can have devastating consequences for even relatively shallow strip mines and quarries. Open-pit mines are deeper than ever before, and because rock mass strength at these large scales is difficult to evaluate, massive slope failure can occur with little warning.
Ground control safety issues are also common hazards that contribute to ground falls. Ground control safety issues include improving roof support, predicting roof conditions, and preventing pillar collapse. Nearly one-third of these accidents occur while removing loose roof and rib rock.
The roof may consist of rock that is inherently low in strength such as drawrock, thinly bedded rock, or mudstone. Discontinuities such as clay veins, slickensides, joints, faults, and paleochannels may also weaken or damage the roof.
The issue
More underground coal reserves are being mined under deeper cover, with potentially dangerous interactions from previous workings. Falls of rock from the roof are one of the leading causes of injuries and fatalities for mine workers.
Common issues with ground falls include:
- Horizontal stress.
- Pillar design.
- Roof support.
- Rock falls.
- Slope stability.
High horizontal stresses produce extensive and sudden rock failures. According to Mine Safety and Health Administration (MSHA) statistics, 27,520 ground control related accidents were reported between 2000 and 2021. These accidents resulted in more than 8,800 injuries to underground workers, including 122 fatal events and 65 instances of permanent disability.
Generally, underground mines use observational techniques to determine roof stability which are not very efficient or accurate. Mine workers usually "sound" the rock—striking it and listening for the "drummy sounds" that signal loose rock. Other techniques include microseismic monitoring, mechanical measurement, load cells, or electromechanical roof monitors.
What's being done
Research relating to a wide range of geologic factors has helped decrease the number of injuries and fatalities from roof falls. NIOSH emphasizes that engineering design should match the appropriate geologic, stress, or mining factors. Convergence and microseismic techniques are also being refined to provide warning of impending roof failures.
NIOSH has been conducting research to develop a better fundamental understanding of ground control strategies. They have addressed the consequences of widening rooms, changing geology and horizontal stress, and different roof support systems.
For example, specialized techniques such as the "advance and relieve" plan have been studied. In this plan, removing a pillar on one side of a panel as the panel advances relieves horizontal stresses. This creates a cave that relieves horizontal stress across the panel.
Analyses of case histories and large-scale testing of roof support have provided many practical ground control techniques.
New tools
A number of tools, particularly classification and test methods, have been and continue to be developed. These include Coal Mine Roof Rating software, ground hazard or condition mapping, diagnosis of moisture sensitivity, and gas content testing.
A Rock Mass Rating was developed in conjunction with the University of Nevada, Reno. The Rock Mass Rating addresses the deficits in rock characterization in those deposits that straddle the classification delineation between rock and soil.
Pillar design
Adequate pillar design is fundamental to maintaining stable underground openings and to providing a safe work environment for underground mine workers.
NIOSH has developed guidelines and criteria for the design of longwall gateroad pillars used in retreat mining. These guidelines are largely based on case histories of pillar performance from a number of mines.
Roof design
NIOSH research developed information and software on the design and performance of various ground support systems including:
- Standing support systems:
- Support Technology Optimization Program (STOP) is software that provides load-displacement guidelines and recommendations for over 100 different types of standing supports.
- Support Technology Optimization Program (STOP) is software that provides load-displacement guidelines and recommendations for over 100 different types of standing supports.
- Intrinsic roof support:
- The Analysis of Roof Bolt Systems software assists in design of roof bolt systems in coal mines.
- The Analysis of Roof Bolt Systems software assists in design of roof bolt systems in coal mines.
- Surface control:
- NIOSH publications have documented the advantages of using roof screen or mesh to prevent ground fall injuries.
- NIOSH publications have documented the advantages of using roof screen or mesh to prevent ground fall injuries.
- Coal Mine Roof Rating:
- The Coal Mine Roof Rating is a rock mass classification system that calculates the inherent strength of coal mine roofs, primarily within the bolted horizon.
- The Coal Mine Roof Rating is a rock mass classification system that calculates the inherent strength of coal mine roofs, primarily within the bolted horizon.
- Stone mine roof span design:
- A survey on roof span issues and design practices discusses the observed factors contributing to roof instability.
- A survey on roof span issues and design practices discusses the observed factors contributing to roof instability.
Software has also been developed for the design of extraction patterns in highwall mining. Other software programs assess bench stability in highly fractured rock slopes that examine plane wedge, step path, and wedge failure modes.
Equipment improvements
The types of injuries related to equipment design range from falls and crushing accidents to repetitive strain like whole-body vibration and overexertion. Some injuries are fatigue related but have not been well-documented or as easy to assess, detect, or predict. The design of both jobs and equipment are often the root causes of injuries.
Both underground and surface mining operations use a variety of production and maintenance equipment, conveyors, and monitoring equipment. The interface between the operator and the equipment is critical to safe and effective operation. Mine workers are sometimes remotely located to their equipment, the equipment is large, and this causes a reduction in the visibility of other workers.
Our research led to the NIOSH-developed shuttle car seat. This seat reduced major jarring and jolting better than any other commercially available seat. The leading manufacturer of shuttle car equipment in the U.S. provides the NIOSH seat as an option in its equipment list.
Training and assessment programs created positive results in the mining industry with the mines that implemented the programs. These interventions grew from the principles and guidelines given in the NIOSH-developed training and demonstrations products.