Key points
- Ensure management is committed to the prevention of work-related musculoskeletal disorders (WMSDs) prevention as well as promoting general safety.
- Get workers involved in identifying and solving ergonomics problems.
- Use a variety of methods to collect input from workers, such as providing direct feedback to conducting company-wide committees.
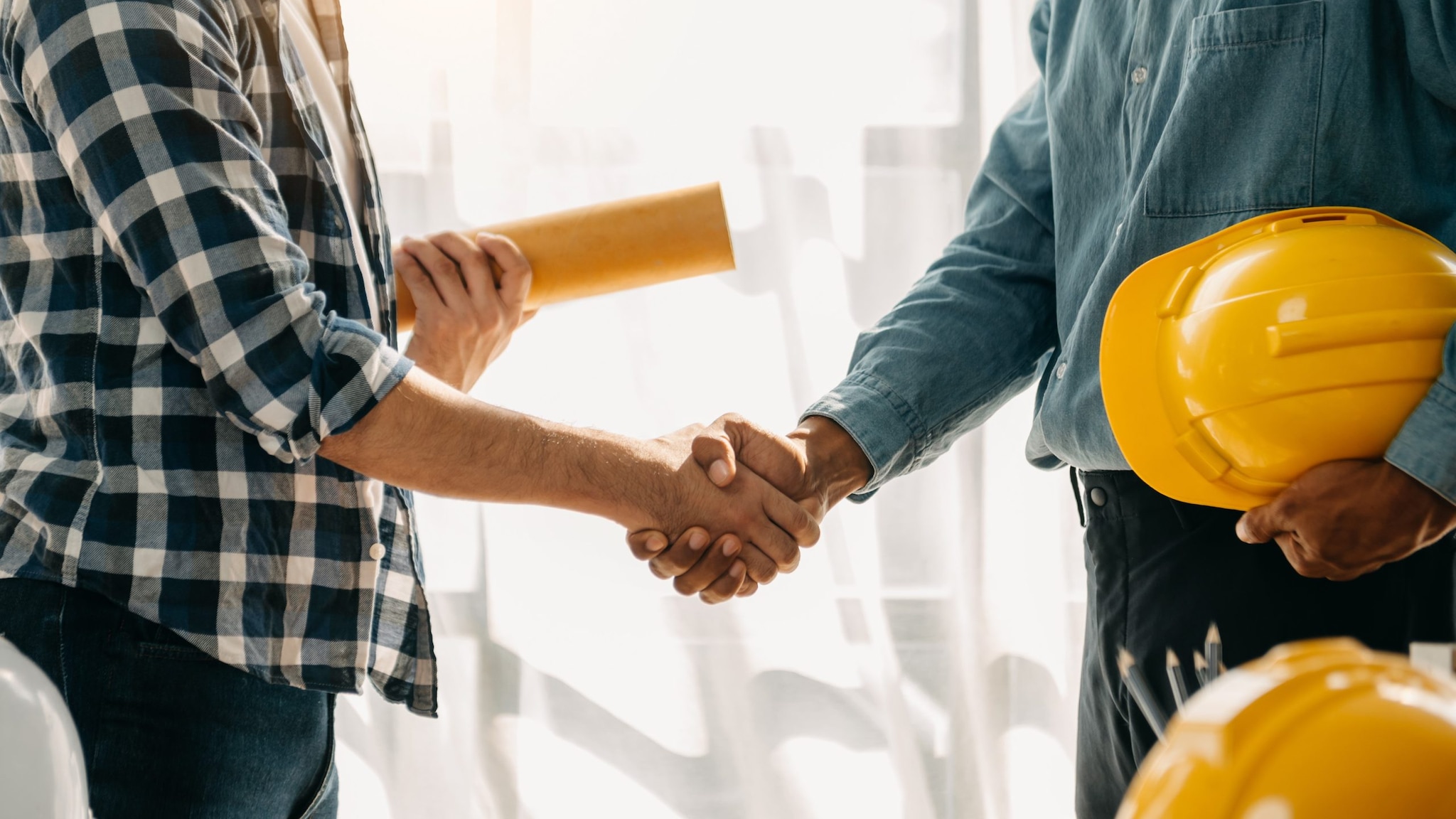
Communicate with management
Occupational safety and health research shows that management commitment is crucial to the success of an intervention. This is especially true for the success of musculoskeletal health awareness training and work-related musculoskeletal disorder (WMSD) prevention interventions.
Management is responsible for encouraging worker input on real or suspected job hazards. They should also seek worker input on ways to control these hazards and how best to implement interventions. Management should follow the objectives of a good ergonomics program, outlined in the figure below.
Management objectives
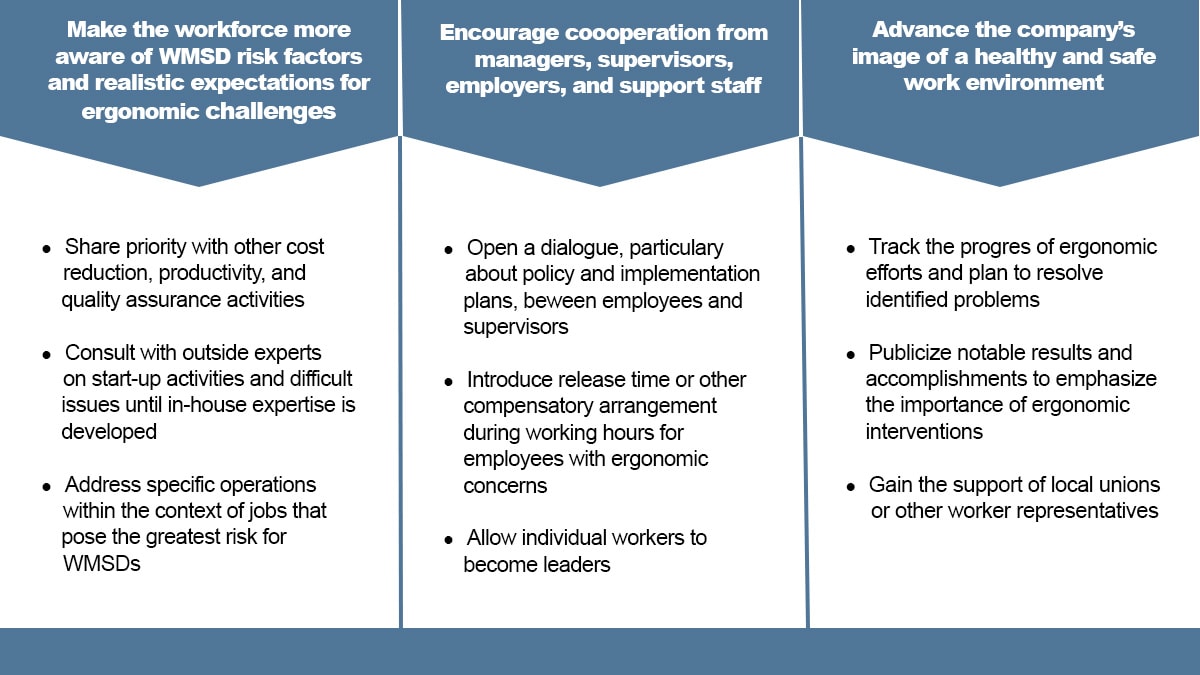
Get employees involved
Ergonomics programs typically require input from worker and management representatives, including:
- Safety personnel
- Health care providers
- Ergonomics specialists
- Human resources
- Maintenance workers
- Engineers
- Purchasing specialists
These groups conduct job analyses, identify hazards, review injury records and symptoms surveys. They also develop control measures and install new equipment specifically for ergonomics programs.
Workers involved in ergonomics programs are trained to recognize physical risk factors. They can then report potential hazards, changes in workplace conditions, and suggestions for improvements.
Workers involved in an ergonomics program show benefits beyond reducing WMSD risks. These workers tend to be:
- More motivated
- Have higher job satisfaction
- Better at problem-solving
- Less resistant to changes in the workplace
- More knowledgeable about their own work
- More connected to the organization for which they work.
Types of worker input
- What worker input looks like
- Individuals communicate their ergonomic concerns to responsible officials
- Maintenance workers, engineering staff and other members of the department should form a ‘work group’ or ‘ergonomics team’ to address issues affecting specific department operations
- Union leaders, worker representatives, department heads, and key figures from various areas of the organization discuss ways to resolve safety and health issues, make recommendations for working groups, and approve resources for specific actions
Examples of worker input
Direct input
NIOSH evaluated WMSD complaints from supermarket cashiers who attributed their pains to certain design characteristics of the checkout counters. Management and workers collectively decided to place a barrier at the far corner of each checkout counter and install adjustable keyboards. The barrier reduced the need for workers to reach for groceries, and the keyboard relieved static stress and shoulder flexion. Reports of MSD symptoms declined after these ergonomic changes were implemented.
Department-wide input
Team members share information related to the WMSD interventions(s) among themselves and with the affected workforce. This is the most popular method of addressing MSD problems.
Company-wide input (committee)
NIOSH assisted an ergonomics committee comprised of:
- One worker and one supervisor from each department.
- One industrial engineer.
- Three manufacturing engineers.
- Three department superintendents.
- One administrative assistant.
- The plant manager.
First, committee members were given literature and videos on ergonomics. Then, the committee examined safety logs, talked with equipment operators, and observed job operations to identify problem areas. Injury patterns, operator reports, and observations indicated specific priorities for intervention.