Preventing Occupational Hearing Loss – A Practical Guide
June 1996
DHHS (NIOSH) Publication Number 96-110
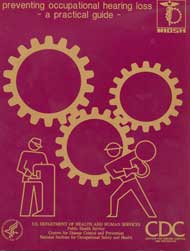
Since the publication of A Practical Guide to Effective Hearing Conservation Programs in the Workplace in 1990, many things have changed, while some have not. Things remaining the same include the Hearing Conservation Amendment to the OSHA Noise Standard. The NIOSH hierarchy of controls endures and can be summarized as: 1) first, prevent or contain the escape of the hazardous workplace agent at its source (engineering control); 2) control exposure by relocating the worker to a safe area (administrative controls); and 3) control the exposure with barriers between the worker and the hazard (personal protective equipment). This hierarchy underscores the principle that the best of all prevention strategies is to have no exposure to agents that can cause or contribute to hearing loss. Corporations that have embarked upon buy-quiet programs are moving towards the creation of a workplace where there will be no harmful noise. Many companies are automating equipment or setting up procedures that can be operated by workers from a quiet control room free from harmful noise, chemical agents, and heat. When it is not possible to remove the harmful agent or relocate the worker to a safe area, the worker must be protected. In the arena of hearing loss prevention, protection is a many-faceted process that includes exposure assessment, provision of protective equipment, assessment of hearing with appropriate management and follow-up actions, worker education and training, and continuous evaluation of program effectiveness.