Asphalt Fume Exposures During the Manufacture of Asphalt Roofing Products
December 1999
DHHS (NIOSH) Publication Number 2000–102
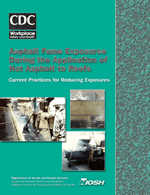
Current Practices for Reducing Exposures
Disclaimer: Mention of any company or product does not constitute endorsement by NIOSH.
Foreword
The Occupational Safety and Health Act of 1970 (Public Law 91–596) assures, insofar as possible, safe and healthful working conditions for every working man and woman in the Nation. The act charges the National Institute for Occupational Safety and Health (NIOSH) with recommending occupational safety and health standards and describing exposure concentrations that are safe for various periods of employment—including but not limited to the concentrations at which no worker will suffer diminished health, functional capacity, or life expectancy as a result of his or her work experience.
This document represents the collaborative efforts of industry, labor, and government to protect the health of workers exposed to asphalt fumes during the manufacture of asphalt roofing products. Current engineering controls and work practices are presented for reducing worker exposures to asphalt fumes during the manufacturing process. These prevention methods are the cornerstone of public and occupational health.
This document is the result of a public meeting convened on July 22 and 23, 1996, in Cincinnati, Ohio. Participants discussed engineering controls and work practices for controlling exposures to asphalt fumes in the roofing industry. Although the health risks from asphalt exposure are not yet fully defined, all partners agreed that prudent action was needed to reduce worker exposures. They decided to produce a joint document which would describe engineering controls and work practices to reduce worker exposure to asphalt fumes during the manufacture of asphalt roofing products. The willingness of all partners to work together in developing this document should serve as a model for others who are developing occupational safety and health recommendations. Development of this document was truly a joint effort. I would like to thank the National Roofing Contractors Association (NRCA), the Asphalt Roofing Manufacturers’ Association (ARMA), and the Asphalt Institute (AI) for their cooperation and hard work.
Linda Rosenstock, M.D., M.P.H., Director
National Institute for Occupational Safety and Health
Centers for Disease Control and Prevention
Abstract
This document represents a collaborative effort of the National Institute for Occupational Safety and Health (NIOSH), the National Roofing Contractors Association (NRCA), the Asphalt Roofing Manufacturers’ Association (ARMA), and the Asphalt Institute (AI) to reduce worker exposures to asphalt fumes during the manufacture of asphalt roofing products. The document describes the manufacturing process, identifies steps in the process with the potential for asphalt fume exposure, and identifies current engineering control methods and work practices used to reduce exposures. In addition, the document lists relevant research needed to further reduce asphalt fume exposures during the manufacture of asphalt roofing products.
Abbreviations
ACGIH | American Conference of Governmental Industrial Hygienists |
AC | asphalt cement |
AI | Asphalt Institute |
AM | arithmetic mean |
APP | atactic polypropylene |
ARMA | Asphalt Roofing Manufacturers’ Association |
BSF | benzene-soluble fraction |
BUR | built-up roofing |
C | degrees Celsius |
CAS | Chemical Abstracts Service |
cfm | cubic feet per minute |
CFR | Code of Federal Regulations |
cm3 | cubic centimeter |
EPA | United States Environmental Protection Agency |
F | degrees Fahrenheit |
Fed. Reg. | Federal Register |
ft2 | square feet |
GM | geometric mean |
GSD | geometric standard deviation |
HHE | Health Hazard Evaluation |
hr | hour(s) |
IARC | International Agency for Research on Cancer |
kg | kilogram |
lb | pound(s) |
LEL | lower explosive limit |
LEV | local exhaust ventilation |
min | minute |
m | meter |
mg | milligram |
ND | not detectable |
ng | nanogram |
NIOSH | National Institute for Occupational Safety and Health |
NRCA | National Roofing Contractors Association |
NSPS | new source performance standards |
OSHA | Occupational Safety and Health Administration |
OV | organic vapor |
PACs | polycyclic aromatic compounds |
PAHs | polynuclear aromatic hydrocarbons |
PAPR | powered air-purifying respirator |
PBZ | personal breathing zone |
PEL | permissible exposure limit |
PPE | personal protective equipment |
REL | recommended exposure limit |
SBS | styrene-butadiene-styrene |
SD | standard deviation |
TLVs® | threshold limit values |
TP | total particulates |
TWA | time-weighted average |
VOC | volatile organic compounds |
% | percent |
Glossary
Air blowing: The manufacturing process used to make oxidized roofing asphalts in which air is blown through an asphalt flux. An exothermic oxidation reaction occurs, yielding an asphalt that is harder, more viscous, less volatile, and less temperature-susceptible than the asphalt flux used as the feedstock to the process.
Asphalt: The product of the nondestructive distillation of crude oil in petroleum refining; it is a dark brown to black cement-like semisolid or solid. Depending on the crude oil used as a feed-stock, the distillation residuum may be further processed, typically by air blowing (sometimes with a catalyst) or solvent precipitation to meet performance specifications for individual applications [AI 1990b]. It is a mixture of paraffinic and aromatic hydrocarbons and heterocyclic compounds containing sulfur, nitrogen, and oxygen [Sax and Lewis 1987].
Asphalt, cutback: An asphalt liquefied by the addition of diluents (typically petroleum solvents) [AI 1990b; Roberts et al. 1996; Speight 1992].
Asphalt flux: The residuum of atmospheric and vacuum distillation processes used by petroleum refineries and independent asphalt manufacturers; used in the manufacture of some asphalt roofing materials (e.g., saturant asphalts, some modified bitumen products); also used as a feed-stock in the air blowing process used to make oxidized roofing asphalt.
Asphalt fumes: The cloud of small particles created by condensation from the gaseous state after volatilization of asphalt [NIOSH 1977].
Asphalt, oxidized (blown or air-refined): Asphalt treated by blowing air through it at elevated temperatures to produce physical properties required for the industrial use of the final product. Oxidized asphalts are used in roofing operations, pipe coating, undersealing for Portland cement concrete pavements, hydraulic applications, membrane envelopes, some paving-grade mixes [AI 1990b], and the manufacture of paints [Speight 1992].
Blowing still: A closed-process vessel, fitted at its base with a sparger, used in the air blowing process to make many types of roofing asphalt.
Built-up roofing (BUR): A system of asphalt-impregnated felt plies sealed and surfaced with hot mopping-grade asphalt, primarily used in low-slope commercial roofing; the felt plies can be organic (e.g., cellulose), fiberglass screen or mat, or polyester fabric.
Coating asphalt: An air-blown or oxidized asphalt used to manufacture inorganic roofing materials used in a variety of roofing systems such as asphalt shingles, polymer-modified bitumen roofing, reinforcing and underlayment felts, and roll roofing products.
Modified bitumen: A roofing system based on membranes manufactured by impregnating or coating one or more fabric plies with a straight-run or oxidized asphalt modified using a polymer, usually atactic polypropylene (APP) or styrene-butadiene-styrene (SBS). Modified bitumen systems may be torch-applied or installed by adhesion in hot asphalt or a cold-applied, solvent-based asphalt adhesive (cutback asphalt). Modified bitumen systems are used on low-slope (primarily commercial or industrial) roofs.
Mopping-grade asphalt: An oxidized asphalt used principally in the construction of BUR and some modified bitumen systems; mopping-grade asphalts are produced in four grades (Types I through IV) according to the steepness of the roof.
Polycyclic aromatic compounds (PACs): A class of chemical compounds that contain two or more fused benzenoid rings. This class of compounds includes polycyclic aromatic hydrocarbons (PAHs) and heterocyclic derivatives in which one or more of the carbon atoms in the benzenoid rings have been replaced by a heteroatom of nitrogen (N-PAC), oxygen (O-PAC), or sulfur (S-PAC) [Vo-Dinh 1989].
Polycyclic aromatic hydrocarbons (PAHs): A class of chemical compounds that only contain carbon and hydrogen in two or more fused benzenoid rings [Vo-Dinh 1989].
Saturant asphalt: A nonoxidized straight-run asphalt or asphalt flux, typically an AC-10 or AC-20 grade material, used to manufacture saturated organic felt plies used in the construction of BUR systems, organic felt shingles, and other roofing materials such as roll roofing.
Straight-run asphalt: The residuum of atmospheric and vacuum distillation processes used in petroleum refineries and by independent asphalt manufacturers. This asphalt used in the manufacture of some asphalt roofing materials (e.g., saturant asphalts, some modified bitumen products); it is also used as a feedstock in the air blowing process used to make oxidized roofing asphalt.
Acknowledgments
This document was prepared by the staff of the National Institute for Occupational Safety and Health (NIOSH) in collaboration with representatives of the Asphalt Institute (AI), the Asphalt Roofing Manufacturers’ Association (ARMA), and the National Roofing Contractors Association (NRCA). The United Union of Roofers, Waterproofers, and Allied Trades reviewed the document. Joann Wess (NIOSH) was the project director.
The contributions of the following staff members are gratefully acknowledged: Tom Calzavara (ARMA); William Candy (ARMA); Bill Fayerweather, Ph.D. (ARMA); Jerome Flesch (NIOSH); Bill Good (NRCA); Jude LaPerouse (NRCA); David Marlow (NIOSH); Bernie McCarthy (AI); Leroy Mickelsen (NIOSH); Dennis Mueller (ARMA); Klaus Rosinski, Ph.D. (ARMA); Arthur Sampson (ARMA); Tom Shanahan (NRCA); Richard Snyder (ARMA); Marie Haring Sweeney, Ph.D. (NIOSH); Alex Teass, Ph.D. (NIOSH); and Ralph Zumwalde (NIOSH).
Vanessa Becks, Richard Carlson, Judy Curless, Susan Feldmann, Anne Hamilton, Susan Kaelin, and Jane Weber (NIOSH) provided editorial support and contributed to the design, graphics, and layout of this document.
1 Introduction
The primary purpose of this document is to increase awareness among plant managers, safety and health professionals, and engineers of the potential for occupational exposure to asphalt and asphalt fumes during the manufacture of asphalt roofing products. The document represents a collaborative effort of industry, labor, and government. During public meetings held in Cincinnati, Ohio (July 22–23, 1996), several groups agreed to develop a series of documents that (1) describe the extent of asphalt exposure during the production of asphalt roofing products and during asphalt roofing operations, and (2) provide information about measures to reduce exposures. These groups included the National Roofing Contractors’ Association (NRCA); the Asphalt Roofing Manufacturers’ Association (ARMA); the Asphalt Institute (AI); the United Union of Roofers, Waterproofers, and Allied Workers; and the National Institute for Occupational Safety and Health (NIOSH). This document identifies work practices and other control measures that, when available, may be effective in reducing worker exposures to asphalt fumes during the manufacture of asphalt roofing products.
Asphalt fumes have been reported to cause irritation of the mucous membranes of the eyes, nose, and respiratory tract [NIOSH 1977]. Other clinical symptoms such as headaches, drowsiness, and loss of appetite have also been reported in workers exposed to asphalt fumes at concentrations below the current NIOSH recommended exposure limit (REL) of 5 mg/m3 (total particulate) as a time-weighted average (TWA) concentration for up to 10 hr/day during a 40-hr workweek [Norseth et al. 1991; Miller and Burr 1996a,b,1998; Hanley and Miller 1996a,b; Almaguer et al. 1996; Kinnes et al. 1996]. Results from recent experimental studies with animals [Niemeier et al. 1988; Sivak et al. 1989, 1997] indicate that roofing asphalt fume condensates generated in the laboratory and applied dermally cause benign and malignant skin tumors in several strains of mice. NIOSH is concerned that workers exposed to asphalt fumes during the manufacture of asphalt roofing products may be at risk for developing chronic health effects, including cancer.
2 Background
2.1 Composition and Uses of Asphalt
Asphalt (CAS* No. 8052–42–4) is a dark brown to black cementitious thermoplastic material found in a natural state, or more commonly, manufactured in petroleum refineries by atmospheric or vacuum distillation; it may also be left as residue after evaporating or otherwise processing crude oil or petroleum. Asphalt is solid or highly viscous at ambient temperatures. This material is an extremely complex mixture containing a large number of high-molecular-weight organic compounds [King et al. 1984]. Asphalt is now the dominant material in roofing in the United States. However, coal tar is still used in some roofing work, usually to conform to government building specifications that require the use of coal tar [Freese and Nichols, Inc. 1994].
*Chemical Abstracts Service.
Most of the asphalt used in the United States is used in paving (87%) and roofing (11%) operations. Only about 1% is used for water-proofing, dampproofing, insulation, paints, and other activities [AI 1990a]. Asphalt roofing products and systems include shingles and roll roofing, ply felt, built-up roofing (BUR) systems, saturated felt used as underlay for shingles, and modified bitumen systems. These products and systems are described in Section 2.4.
2.2 Manufacture of Asphalt Roofing Products
Ninety-seven asphalt roofing manufacturing plants currently operate in the United States. These plants are owned by 27 companies and are located in 28 States, generally within 500 to 800 miles of their primary markets. The plants vary greatly in size, number of workers, and products manufactured. A typical asphalt roofing plant manufactures several products, including shingles, roll roofing (smooth or mineral surfaced), ply felt for use in BURs, and saturated felt used as underlay for shingles. Modified bitumen products are manufactured on machines designed for polymer-modified materials.
The estimated number of workers in the asphalt roofing manufacturing industry is 10,000 [ARMA 1999].
2.3 Manufacture of Roofing Asphalts
Petroleum refineries and independent asphalt manufacturers produce roofing asphalt by air blowing the residuum of refinery atmospheric or vacuum distillation processes. This residuum is blended to “asphalt flux.” In the air blowing or oxidation process, asphalt flux is placed into a tank known as a blowing still and heated while air is blown through it. The temperature and the amount of air are varied by the manufacturer depending on the nature of the asphalt flux and the intended characteristics of the roofing asphalt being produced. This process raises the softening point and viscosity and lowers the penetration and ductility of the asphalt [King et al. 1984; IARC 1985].
At the temperatures of the air-blowing process (400 to 600° F [204 to 316° C]) [Shell 1995], the oxidation reactions ultimately yield (1) compounds of higher molecular-weight through ester and carbon-carbon bond formation from oxidation intermediates, (2) compounds of increased unsaturation through oxidative dehydrogenation, and (3) smaller molecules produced by cleavage of side chains from larger molecules [Shell 1995; Goppel and Knotnerus 1995]. A significant portion of the relatively volatile components of the original asphalt and of those produced during the process are probably removed in the effluent. The air-blown asphalts contain an increased proportion of asphaltenes, but decreased proportions of the resins, oils, and waxes [Speight 1992]. Compared with its precursor, the components of air-blown asphalt have a higher average molecular weight. Also, during the air blowing process, relatively volatile components and products are removed. These observations lead to the conclusion that the air-blown asphalt will produce fume at a slower rate than its precursor when heated to the same temperature. These same observations do not allow conclusions regarding the content of that fume.
The three basic grades of roofing asphalt are (1) saturant grade asphalt, a raw material used to manufacture saturated inorganic and organic felt plies used in the construction of BUR systems, organic felt shingles, and other roofing materials such as roll roofing; (2) coating grade asphalt, a raw material used to manufacture inorganic roofing materials for a variety of roofing systems such as asphalt shingles, polymer-modified bitumen roofing, reinforcing and underlayment felts, and roll roofing products; and (3) mopping-grade asphalt, an end product that is melted and used in the construction of BUR and modified bitumen systems. Each grade of asphalt is also used to manufacture a variety of asphalt coating and sealant products.
The principal differences between saturant and coating-grade asphalts are viscosity and softening point. Saturant asphalts typically have a softening point of about 120 to 140° F (50 to 60° C), making them less viscous than coating asphalts, which have a softening point of approximately 200 to 225° F (95 to 105° C). Despite their lower viscosity, saturant asphalts are processed at significantly higher temperatures (about 425 to 475° F/218 to 245° C) than coating asphalts (about 380 to 460° F/190 to 238° C) because of the need to ensure adequate impregnation of the organic felts that use saturant asphalts [ASTM 1995].
The four types of mopping-grade asphalt are described in Table 2—1. The viscosity of mopping-grade asphalts depends on which of the four types is being manufactured. Type I is the softest (least viscous) grade and is used on very-low-slope roofs. Type IV is the hardest (most viscous) grade and is used on the highest slope roofs suitable for BUR systems.
2.4 Asphalt Roofing Products and Systems
Today, three commercially popular roofing products or systems are made from roofing asphalt, each with different characteristics and applications:
Table 2—1. Types of mopping-grade asphalt
Type | Susceptibility to flow at roof temperatures | Highest slope suitable for use (% slope) | Softening point (°F) | |
---|---|---|---|---|
I | dead level | Relatively susceptible | 2 | 135–151 |
II | flat | Moderately susceptible | 4 | 158–176 |
III | steep | Relatively nonsusceptible | 25 | 185–205 |
IV | special steep | Relatively nonsusceptible | 50 | 210–225 |
- Asphalt shingles and roll roofing are used in residential and steep-slope commercial roofing.
- BUR systems are asphalt-impregnated felt pieces sealed and surfaced with hot mopping asphalt; the systems are used in low-slope commercial roofing.
- Modified bitumen systems are also a low-slope commercial product using polymer-modified roofing asphalts to impregnate and coat one or more fabric plies.
2.4.1 Asphalt Shingles and Roll Roofing
Asphalt shingles introduced in the early 1900s account today for about 75% of new construction and reroofing in steep-slope residential and some commercial roofing applications [NRCA 1995]. Roll roofing was the mainstay of the steep-slope market until it was largely displaced by shingle products. Today, roll roofing is used mainly in BUR systems on low-slope roofs. With low-slope roofing, smooth-surface roll roofing can be used in building the BUR membrane, and mineral-surfaced roll roofing is used as a cap or “top sheet” [NRCA 1996; AI 1990a].
Asphalt shingles and roll roofing both consist of a reinforcing felt covered with coating asphalt; organic felts are impregnated with a saturant asphalt. In most cases, asphalt shingles and roll roofing contain a surfacing material, usually coarse or fine mineral. Asphalt shingles and roll roofing are installed using mechanical fasteners or cold-applied adhesives; they do not require hot mopping asphalt. In addition, are typically installed over an underlayment felt that has been impregnated with coating asphalt during manufacture, and both are affixed to the roof substrate by mechanical means or cold adhesives [NRCA 1996].
2.4.2 Built-Up Roofing Systems
BUR systems were introduced in the late 1800s and remain the most popular roofing system for commercial and industrial buildings, accounting for about 30% of the new and retrofit market for low-slope roofs [NRCA 1995]. The BUR membrane is composed of layers (or “moppings”) of mopping asphalt, between felt plies of saturant asphalt or coating asphalt reinforcing fabric, such as organic felts (e.g., cellulose), fiberglass scrim or mat, or polyester fabric. BUR membranes are installed in multiple-ply configurations that typically involve three to six interply moppings of mopping asphalt. In addition, roll roofing made from organic or inorganic materials, or a flood coat† of mopping asphalt (usually Type I) is applied as a weatherproofing top layer.
†Flood coat is the surfacing layer of asphalt into which surfacing aggregate is embedded on an aggregate-surfaced built-up roof. A flood coat is generally thicker and heavier than a glaze coat and is applied at approximately 45 to 60 lb/100ft2 (a square) (2 to 3 kg/m2).
All three grades of roofing asphalt (coating, saturant, and mopping) may be used in the manufacture or construction of BUR systems: saturant asphalts are used to manufacture organic felts and roll roofing; coating asphalts are used for virtually all felt ply and roll goods; and heated mopping asphalts are used for the interply moppings and, in some cases, the flood coats applied in constructing the BUR membrane [NRCA 1996].
2.4.3 Modified Bitumen Roofing Systems
Polymer-modified bitumen roofing systems were introduced in the 1970s and today account for about 23% of the new and retrofit market for low-slope (i.e., primarily commercial and industrial) roofs [NRCA 1995]. Modified bitumen products are of two types: (1) those made primarily with atactic polypropylene (APP), and (2) those made primarily with styrene-butadiene-styrene (SBS) as the polymer modifier.
APP membranes are primarily torch-applied— that is, they are adhered to an underlying base sheet or to the manufacturer’s approved substrate by heating the back side of the APP membrane and the substrate with high-intensity, propane-fired torches or specially designed hot-air welders. The heat is applied only as needed to soften the asphalt and make the modified bitumen membrane adhere to the substrate; these products can be cold-applied with adhesives. SBS membranes may be applied by adhesion in hot asphalt, in a cold-applied solvent-based asphalt adhesive, or torch-applied [NRCA 1996].
3 Manufacture of Asphalt Roofing Products
3.1 Primary Manufacturing Processes
The manufacture of asphalt roofing products consists of six major operations: (1) felt saturation, (2) coating, (3) mineral surfacing (top and bottom), (4) cooling and drying, (5) product finishing (seal-down strip application, cutting and trimming, and laminating of laminated shingles), and (6) packaging. The six major production support operations are as follows: (1) air blowing, (2) delivery, in-plant transfer, and storage of hot asphalt, (3) back surfacing and granule storage, (4) filler storage, (5) filler heating, and (6) filler and coating asphalt mixing. Figure 3—1 shows a typical manufacturing line for an asphalt roofing product. The following sections give detailed descriptions of the major processes associated with the manufacture of asphalt roofing products.
3.1.1 Air Blowing
Preparing the roofing asphalt is an integral part of manufacturing asphalt roofing products. This preparation, called blowing or air blowing, involves bubbling air through liquid asphalt flux in blowing stills. Blowing stills are closed process vessels located out-of-doors. Emissions from the vessels are vented to capture devices located away from work areas and do not require continuous or frequent attendance by workers (see Figure 3—2). Blowing operations may be located at oil refineries, asphalt processing plants, or asphalt roofing products plants.
A blowing still is a tank fitted near its base with a sparger (air lines in a spider arrangement). The purpose of the sparger is to increase contact between the air and the asphalt. Air is forced through holes in the sparger into a tank of hot asphalt flux. The air rises through the asphalt, resulting in an exothermic oxidation reaction.
Sometimes a catalyst such as ferric chloride is added to assist in this transformation. Because of the exothermic nature of the reaction, the temperature may reach 500° F (260° C) and require the installation of an overhead water spray inside the still to prevent combustion of the material. Such temperature control also prevents thermal cracking of the chemical constituents of the asphalt.
Air blowing the asphalt raises its softening temperature and reduces its penetration, resulting in a “harder,” more viscous asphalt suitable for roofing applications.
3.1.2 Supporting Operations
Asphalt is normally delivered in bulk to the asphalt roofing plant by pipeline, tanker truck, or railcar. Bulk asphalts are delivered in liquid form at temperatures of 200 to 400° F (93 to 204° C), depending on the type of asphalt and local practice.
Several tanker unloading techniques are used. The most common method is to couple a flexible pipe to the tanker and pump the asphalt directly into the appropriate storage tanks. Another unloading procedure is to pump the hot asphalt into a large, open funnel connected to a surge tank. From there, asphalt is pumped into storage tanks.
Asphalt flux (see Section 2.3) is usually stored at 124 to 174° F (51 to 79° C), although storage temperatures of up to 450 F (323 C) have been noted. Lower temperatures of the asphalts are usually maintained with steam coils in the tanks. Saturant and coating asphalt are normally stored at 400 to 500° F (204 to 260° C). Temperatures are maintained by heating the tanks directly or by cycling the asphalt through external heat exchangers, usually of the closed-tube type. Asphalt is transferred within the plant by closed pipeline.
Figure 3—1. Diagram of typical manufacturing line for an asphalt roofing product. (Source: EPA [1988].)
Figure 3—2. Preparation of roofing asphalt by air blowing. (Source: EPA [1988].)
3.2 Manufacturing Line
The following sections provide detailed descriptions of the manufacturing processes for roofing asphalt products and product groups.
3.2.1 Saturant Asphalt Felt
Saturant asphalt felt is the most basic asphalt roofing product. Figure 3—3 depicts a typical manufacturing line for asphalt-saturated felt. It consists of a dry felt feed roll, a dry looper section, a saturator spray section, a saturator dipping section, heated drying-in drums, a wet looper, a finish floating looper, and a roll winder.
Organic felt may weigh from approximately 20 to 55 lb/480 ft2 (a common unit in the paper industry), depending on the intended product. The felt is unrolled from the unwind stand onto the dry looper, which maintains a constant tension on the material. The dry floating looper provides a reservoir of web material to match the intermittent operation of the roller to the continuous operation of the line.
From the dry looper, the felt may pass into the spray section of the saturator (not used in all plants), where saturant asphalt at 400 to 480° F (205 to 250° C) is sprayed onto one side of the felt through several nozzles. In the saturator dip section, the saturated felt is drawn over a series of rollers, with the bottom rollers submerged in hot saturant asphalt at 400 to 480° F (205 to 250° C).
During the next step, the heated drying-in drums press saturant asphalt into the felt. Occasionally, additional saturant asphalt is added at this point. The wet looper increases absorption by providing sufficient time for the saturant asphalt to penetrate the felt.
The saturated felt then passes through water-cooled rolls onto the finish floating looper. These steps allow the felt to cool and serve as an accumulator to match the continuous operation of the line to the intermittent operation of the roll winder. Finally, the felt is rolled and cut to size on the roll winder. Common weights of saturant felt are approximately 15 to 50 lb/108 ft2 of saturant felt (which covers exactly 100 ft2 of roof).
3.2.2 Asphalt Shingles and Roll Goods
Figure 3—4 illustrates the typical manufacturing process for producing organic asphalt roofing shingles, mineral-surfaced rolls, and smooth rolls. For organic products, the initial processing steps are similar to the saturant asphalt felt line just described and include the saturator and wet looper. Organic felt products pass to the saturator and then, in some plants, on to a coater (see Figure 3—4).
Figure 3—3. Typical flow diagram for the production of saturant asphalt felt. (Source: EPA [1988].)
Figure 3—4. Typical flow diagram for the production of organic asphalt roofing shingles and rolls. (Source: EPA [1988].)
The coater employs a roller type system to apply a stabilized coating asphalt to the top and bottom surfaces of the webbing sheet. Stabilized coating asphalt is harder, more viscous asphalt, which has a higher softening point than saturant asphalt and a mineral stabilizer*. The mineral stabilizer may consist of finely divided lime, silica, slate dust, dolomite, or other mineral materials. The softening point of saturant asphalts varies from 104 to 165° F (40 to 74° C), whereas the softening point of coating asphalt varies from 210 to 240° F (99 to 116° C).
*The mineral stabilizer used in asphalt roofing applications is an inorganic material, typically a crushed rock. Because this material is inorganic, it is less susceptible to temperature change and fire. These properties are important for shingle manufacturing. Asphalt with stabilizer is uniform and consistent within the climatic temperature range. Essentially, the stabilizer reduces viscosity in colder weather (making the shingle less brittle) and increases viscosity in warmer weather (increasing the softening point). In addition, the mineral stabilizer decreases the flammability of asphalt, thus allowing a higher fire rating of the shingle.
The “filled” or “stabilized” coating asphalt applied during the coater operation is made in the coater-mixer, which is usually positioned above the manufacturing line at the coater. Coating asphalt at 325 to 400° F (163 to 205° C) is piped into the mixer and the mineral stabilizer is delivered by screw conveyor. To eliminate moisture problems and to help maintain the temperature above 360° F (182° C) in the coater-mixer, the mineral stabilizer is dried and preheated before being fed into the coater-mixer.
The weight of the finished product is controlled by the amount of coating asphalt used. The coater rollers can be moved closer together to reduce the amount of coating asphalt applied to the felt or separated to increase it. Most modern plants are equipped with automatic scales or profile scanners that monitor the sheets during the manufacturing process and warn the coater operator when the product is running under or over specifications.
Colored granules are applied in a section of the manufacturing line that usually consists of a multi-compartmented granule hopper, two parting agent hoppers, and two large press rollers. The hoppers are fed through flexible hoses from one or more machine bins above the line. These machine bins (sometimes called surge bins) provide temporary storage. The granule hopper drops colored granules from its various compartments onto the top surface of the moving sheet of coated webbing in the sequence necessary to produce the desired color pattern on the roofing. Parting agents such as talc and sand are applied from parting agent hoppers to the back surface of the coated sheet. Smooth-surfaced products do not require the application of colored granules. Talc or sand is usually applied to both sides when smooth roll roofing is made.
The next step is product cooling and seal-down strip application. As in the case of the saturated felt line, the sheet is cooled rapidly by passing it around water-cooled rollers in an abbreviated looper arrangement. Usually, water is also sprayed on the surfaces of the sheet to speed this cooling process.
Subsequently, the asphalt seal-down strip is applied to self-sealing coated roofings by a roller partially submerged in a pan of hot sealant asphalt that is usually covered. Extrusion is another method of seal-down application. Some products are also texturized at this point by passing the sheet over an embossing roll that forms a pattern in the surface of the sheet. The final steps in the production of asphalt roofing shingles and roll roofing are the finish or cooling looper (which is essentially the same process used for saturated felts), followed by cutting and packaging. The sheet destined for roll roofing is wound on a mandrel, cut to the proper length, and packaged. When shingles are made, the material from the finish looper is fed into the shingle cut machine. After the shingles have been cut, they are usually moved by roller conveyor to automatic packaging equipment, although manual packaging is still used for some shingle products. The packaged shingles are then stacked on pallets and transferred by forklift to storage areas or waiting trucks.
For fiberglass products, which today make up about 85% of the asphalt roofing shingle market and more than 90% of the ply sheets used in BUR, the initial saturation operation is eliminated. As shown in Figure 3—5, the manufacture of fiberglass roofing products begins (as do organic felts) with the feeding of the mat through a dry looper and then it proceeds to a coater.
3.2.3 Modified Bitumen Products
The manufacturing line for modified bitumen products is similar to that used for organic asphalt roofing shingles and roll roofing. A diagram for the production of modified bitumen products appears in Figure 3—6.
The first step in the manufacture of modified bitumen products is mixing the asphalt with either atactic and isotactic polypropylene or styrene-butadiene-styrene and a mineral stabilizer in large heated tanks (356° F/180° C). This mixture is then applied in an impregnation vat to a polyester and/or fiberglass mat base webbing. (The impregnation vat consists of a looper-type arrangement in a shallow vat of the asphalt mixture and a set of rollers that meter the thickness of the product.) During the cooling process, either a polypropylene backing or granules are applied to the top side of a sheet (which is still hot) floating on a water-filled tray. The sheet is then either completely submerged in another water-filled tray or sprayed with water to finish the cooling process. After the sheet is dried with a fan, talc or sand is applied to the under-surface side as a parting agent. The sheet then passes through a finish looper (accumulator) and is wound on rolls.
Figure 3—5. Typical flow diagram for the production of fiberglass shingles and rolls (Source: ARMA [1997].)
Figure 3—6. Diagram for the production of modified bitumen product. (Source: EPA [1988].)
4 Occupational Exposure to Asphalt Fumes
4.1 Occupational Exposure Limits
Currently, no Occupational Safety and Health Administration (OSHA) standard exists for asphalt fumes. In 1989, OSHA announced that it would delay a final decision to establish a permissible exposure limit (PEL) for asphalt fumes because of complex and conflicting issues submitted to the record [54 Fed. Reg.* 2679]. OSHA originally proposed a PEL of 5 mg/m3 as an 8-hr TWA to reduce the risk of cancer from occupational exposure to asphalt fumes. In 1992, OSHA published another proposed rule for asphalt fumes that included a PEL of 5 mg/m3 (total particulates) for general industry and for the maritime, construction, and agricultural industries [57 Fed. Reg. 26182]. OSHA is still receiving comments but has not yet published a schedule for a course of action.
*Federal Register. See Fed. Reg. in references.
In 1977, NIOSH established an REL of 5.0 mg/m3 (total particulate) for asphalt fumes measured as a 15-min ceiling to protect against irritation of the serous membranes of the conjunctivae and the mucous membranes of the respiratory tract. The conclusions of the 1977 document stated that “although no experiment clearly demonstrated a direct carcinogenic hazard associated with asphalt fumes, NIOSH is concerned that future scientific investigations may indicate a greater occupational hazard from asphalt fumes than is currently documented in the literature” [NIOSH 1977]. Since publication of the criteria document, studies concerning the chronic effects of laboratory-generated asphalt fumes on experimental animals have produced evidence of carcinogenicity. In 1988, NIOSH (in testimony to the Department of Labor) and OSHA recommended that asphalt fumes be considered a potential occupational carcinogen [NIOSH 1988]. This recommendation was based on information presented in the Niemeier et al. [1988] study. NIOSH is currently re-evaluating the health data.
The current American Conference of Governmental Industrial Hygienists (ACGIH) threshold limit values (TLVs) for asphalt fumes is 5.0 mg/m3 (total particulate) [ACGIH 1999] with an A4 designation, indicating that it is not classifiable as a human carcinogen [ACGIH 1999]. However, in the notice of intended changes for 1999, an 8-hr TWA TLV of 0.5 mg/m3 as benzene-extractable inhalable particulate (or equivalent method) was proposed for asphalt fumes; the A4 designation remains.
4.2 Potential for Exposure
Dermal contact with hot asphalt can cause burns, and asphalt fumes or vapors can be absorbed through the skin. Information is limited on the occurrence of exposure to asphalt fumes during the manufacture of asphalt roofing products. Five NIOSH health hazard evaluations (HHEs) conducted during the 1970s listed personal breathing zone (PBZ) concentrations ranging from 0.3 to 32 mg/m3 for total particulates and 0.21 to 6.8 mg/m3 for the cyclohexane solubles [Apol and Okawa 1977, 1978; Okawa and Apol 1977, 1978a,b] (see Table 4—1). In a cross-sectional exposure assessment study conducted for the AI [AI 1991; Hicks 1995], data indicate that PBZ measurements ranged from 0.068 to 13 mg/m3 for total particulates; PBZ measurements ranged from 0.013 to 3.7 mg/m3 for benzene solubles [AI 1991; Hicks 1995] (see Table 4—1).
An analysis of the 34 full-shift PBZ samples (most sampling ranged from 7 to 9 hr) indicates that the geometric mean (GM) for total particulates is 1.4 mg/m3, and the GM for benzene solubles is 0.27 mg/m3 [Hicks 1995] (see Table 4—2). In another study [Exxon 1997], analysis of 77 PBZ samples indicates that the GM for total particulates is 0.6 mg/m3; the GM for the benzene-soluble fraction of the samples was 0.08 mg/m3.
In the Hicks [1995] study, dermal wipe samples were collected at the end of the work shift from either the forehead or the back of the hand from 29 workers wearing air sampling equipment. All samples were analyzed for chrysene, dibenz(a,h)-anthracene, fluoranthene, naphthalene, indo-(1,2,3–cd)pyrene, and phenanthrene. Only naphthalene (<5.5 to 160 ng/cm2), indo-(1,2,3–cd)pyrene (<4.5 to 25 ng/cm2), and phenanthrene (2.4 ng/cm2) were identified in appreciable amounts.
The asphalt roofing products manufacturing industry summarized exposure data collected during 1980–1997 at 53 plants of 4 companies (A, B, C, D). The data were from 1,920 samples for total particulates and 1,184 samples for benzene or cyclohexane solubles as TWAs [Fayerweather 1998]. Exposure data were not provided by job title because job titles were inconsistent among companies and did not always relate to a location or task on the manufacturing line. An attempt to classify the jobs into three exposure groups was unsuccessful because sampling was reported to have been conducted during nonroutine tasks and conditions. Figures 4—1 and 4—2 compare the average exposure data for total particulates and benzene/cyclohexane solubles for 1980–1989 and 1990–1997 from the four companies. (No comparison data were available for company D since data were collected only for 1995–1997.) These figures indicate that average exposures, expressed as either total particulate or benzene/cyclohexane solubles, have declined after 1990 for companies A, B, and C.
No conclusions can be drawn as to the statistical significance of this observation, however, since statistical analyses were not conducted and raw data are not available for additional analyses.
The asphalt roofing manufacturing industry attributes this apparent reduction in average exposures after 1990 to the following: (1) the elimination of the saturator process by converting from paper roofing felts to glass fiber mats, (2) the improvement of capture efficiency of exhaust hoods, (3) the conversion to closed saturators on several operations, and (4) reducing fugitive emissions subject to EPA regulations under the new source performance standards (NSPS) and other 1990 Clean Air Act Amendment requirements. By 1990, most plants had eliminated the saturator process and implemented other controls (not specified) [Trumbore et al. 1992; Keating and Vermilion 1995].
Table 4—1. Asphalt fume exposures for various occupations during manufacturing of roofing products
Breathing-zone samples | Exposure concentration (mg/m3) | ||||
---|---|---|---|---|---|
Reference, source of exposure, and occupation | Type † | Number | Range | Geometric Mean | Arithmetic Mean |
Apol and Okawa [1977], production of asphalt shingles and rolled roofing materials: | |||||
Saturator operator | Total particulates Cyclohexane solubles |
3 2 |
2.2-7.3 0.81-2.6 |
4.9 1.4 |
5.6 1.7 |
Coater operator | Total particulates Cyclohexane solubles |
2 2 |
14-15 0.87-6.8 |
14 2.4 |
14 3.9 |
Coater trainee | Total particulates Cyclohexane solubles |
2 2 |
11-15 0.30-2.3 |
13 0.84 |
13 1.3 |
Press operator | Total particulates Cyclohexane solubles |
2 2 |
6.1-32 1.4-1.5 |
14 1.4 |
19 1.42 |
Seal down operator | Total particulates Cyclohexane solubles |
2 2 |
0.99-1.4 0.43-1.2 |
1.2 0.71 |
1.21 0.81 |
Foreman | Total particulates Cyclohexane solubles |
2 2 |
5.3-6.3 0.47-0.53 |
5.8 0.50 |
5.8 0.5 |
Laminator operator | Total particulates Cyclohexane solubles |
7 5 |
0.96-2.16 0.23-0.76 |
1.6 0.46 |
1.6 0.50 |
Okawa and Apol [1977], production of asphalt shingles: | |||||
Laminator operator | Total particulates Cyclohexane solubles |
8 8 |
0.38-5.2 0.24-3.1 |
1.0 0.76 |
1.4 1.05 |
Saturator/Coater | Total particulates Cyclohexane solubles |
6 6 |
5.3-29 0.66-1.3 |
8.03 0.88 |
12 0.91 |
Apol and Okawa [1978], production of asphalt shingles and rolled roofing materials: | |||||
Saturator operator | Total particulates Cyclohexane solubles |
1 1 |
* * |
2.4 0.76 |
2.4 0.76 |
Coater | Total particulates Cyclohexane solubles |
2 2 |
12-16 0.21-1.1 |
14 0.47 |
14 0.64 |
Wrapping machine operator | Total particulates Cyclohexane solubles |
1 1 |
* * |
1.4 0.77 |
1.40 0.77 |
*See footnotes at end of table. (Continued)
Table 4—1 (Continued). Asphalt fume exposures for various occupations during manufacturing of roofing products
Breathing-zone samples | Exposure concentration (mg/m3) | ||||
---|---|---|---|---|---|
Reference, source of exposure, and occupation | Type † | Number | Range | Geometric Mean | Arithmetic Mean |
Apol and Okawa [1978], continued: Lead man |
Total particulates Cyclohexane solubles |
1 1 |
* * |
5.3 0.76 |
5.29 0.76 |
Presser | Total particulates Cyclohexane solubles |
2 2 |
8.3-22 0.30-0.54 |
13 0.402 |
15 0.42 |
Okawa and Apol [1978a], production of asphalt shingles and rolled roofing materials: | |||||
Coater | Total particulates Cyclohexane solubles |
2 2 |
4.2-5.1 3.3-3.9 |
4.6 3.6 |
4.7 3.6 |
Cooling section operator | Total particulates Cyclohexane solubles |
2 2 |
0.3-1.0 0.7-1.6 |
0.55 1.06 |
0.65 1.2 |
Machine tender | Total particulates Cyclohexane solubles |
2 2 |
0.4-2.8 0.6-1.8 |
1.06 1.04 |
1.6 1.2 |
Okawa and Apol [1978b], production of asphalt shingles and rolled roofing materials: | |||||
Saturator operator | Total particulates Cyclohexane solubles |
1 1 |
* * |
1.0 2.1 |
1.0 2.1 |
Coaterman | Total particulates Cyclohexane solubles |
1 1 |
* * |
2.1 0.22 |
2.1 0.22 |
Slateman | Total particulates Cyclohexane solubles |
1 1 |
* * |
3.4 0.21 |
3.4 0.21 |
Pozzoli et al. [1985], asphalted paper production: | |||||
Paper production workers (smokers) |
Total PAHs | 4 | 0.0048-0.036 | 0.009 | 0.014 |
Paper production workers (nonsmokers) |
Total PAHs | 2 | 0.0034-0.311 | 0.010 | 0.017 |
*See footnotes at end of table. (Continued)
Table 4—1 (Continued). Asphalt fume exposures for various occupations during manufacturing of roofing products
Breathing-zone samples | Exposure concentration (mg/m3) | ||||
---|---|---|---|---|---|
Reference, source of exposure, and occupation | Type † | Number | Range | Geometric Mean | Arithmetic Mean |
AI [1991]; Hicks [1995], Roofing manufacturing (temperature of product at fume source from 300-700 F): | |||||
Loader/asphalt handler | Total particulates Benzene solubles |
6 6 |
0.068-0.94 0.041-0.71 |
0.51 0.31 |
0.66 0.41 |
Slate blend operator | Total particulates Benzene solubles |
4 4 |
1.1-13 0.013-0.94 |
3.9 0.077 |
5.6 0.27 |
Coater operator | Total particulates Benzene solubles |
8 8 |
0.42-2.5 0.049-1.6 |
1.0 0.2 |
1.3 0.37 |
Machine operator | Total particulates Benzene solubles |
8 8 |
0.8-4.4 <0.071-3.6 |
1.6 0.55 |
1.9 1.5 |
Press operator/cooling operator |
Total particulates Benzene solubles |
7 7 |
0.55-11 <0.085-3.7 |
2.6 0.32 |
4.8 1.0 |
Supervisor | Total particulates Benzene solubles |
1 1 |
* * |
1.4 0.32 |
1.4 0.32 |
* Information not provided.
†The sampling and analytical methods used for measuring benzene solubles and PAH concentrations may vary between studies and these results may not be directly comparable.
Table 4—2. Exposures during manufacture of asphalt roofing products
Concentration (mg/m3) | ||||
---|---|---|---|---|
Sample type | Range | Geometric mean (GSD)* | Arithmetic mean (SD) | Median |
Total particulates | 0.068-13 | 1.4 (3) | 2.6 (3.1) | 1 |
Benzene-soluble fraction | <0.071-3.7 | 0.27 (4.4) | 0.76 (1.1) | 0.24 |
Source: Adapted from Hicks [1995].
*Abbreviations: GSD = geometric standard deviation; SD = standard deviation.
Figure 4—1. Total particulate levels pre- and post-1990 by company. (Source: Fayerweather [1988].)
Figure 4—2. Benzene/cyclohexane solubles pre- and post-1990 by company. (Source: Fayerweather [1988].)
4.3 Operations and Jobs with Potential for Asphalt Fume Exposure
The basic manufacturing process for all asphalt roofing products is essentially the same, with slight modifications, depending on which product is being produced. Figure 3—1 presents the diagram of a typical asphalt roofing manufacturing line.
The operations that pose a potential for worker exposure to asphalt fumes involve hot liquid asphalt. These operations include the following:
- The delivery, in-plant transfer, and storage of asphalt flux and the various roofing asphalts used in the manufacturing process
- Unloading techniques—coupling flexible pipe to tanker and pumping hot asphalt into appropriate storage tanks
- Pumping hot asphalt into large open funnel connected to surge tank, then pumping hot asphalt into storage tanks
- Incorporating mineral stabilizers to coat asphalts and, in the case of modified asphalt products, to blend polymers in mixing tanks
- Using the coater, or the impregnation vat in the case of modified bitumen products, where liquid coating asphalt is applied to the surfaces of the felts
- Using the saturator, which is used before or in lieu of coating in the case of organic felts, where the felts are sprayed with and then immersed in a saturant asphalt
- Conducting quality control activities associated with testing raw materials
- Conducting production activities with line breaks requiring maintenance
- Conducting off-line laminator operations where hot asphalt is heated and applied between two or three layers of shingles
Guidelines for Protecting Workers
This section describes available engineering controls, work practices, and personal protective equipment (PPE) used to reduce worker exposure to asphalt fumes in the roofing manufacturing industry. Engineering controls include process substitution, isolation (enclosures), and general and local exhaust ventilation. Some of these methods may be used for other purposes, such as energy conservation or compliance with other regulatory requirements. Information is provided on available engineering controls and work practices to reduce worker exposure to asphalt fumes for operations and jobs identified in Section 4.3.
5.1 Delivery, Handling, and Storage
The following engineering controls are used to reduce worker exposure to asphalt fumes during the delivery, handling, and storage of hot asphalt.
5.1.1 Engineering Controls
Typically, a variety of tanks are used to contain hot asphalt in asphalt roofing manufacturing plants. These include storage tanks for delivered asphalt, saturant asphalts, and coating asphalts to be used in the production process; polymer and stabilizer mixing tanks in which asphalt coatings are made for conventional asphalt and modified bitumen roofing products; smaller-scale heating tanks for specialty operations such as laminating; and finished product tanks in plants that produce roofing asphalt for sale or shipment elsewhere.
Studies to determine the effectiveness of the following controls are necessary. Available engineering controls for reducing asphalt fume exposures include closed tanks. Asphalt fumes generated in these tanks may be vented directly to either the outside atmosphere or to one of several types of fume capture devices. Typical capture devices that can reduce the concentration of asphalt fumes and dusts released from these tanks or from blowing stills, coaters, and saturators include, but are not limited to, the following:
- Mist eliminators: use screening or coarse filter media (usually a permanent metal pad type) to remove droplets contained in the air steam.
- High-velocity air filters or fiberbed filters: use disposable filter media to initiate condensation of condensable portions of the air steam.
- Electrostatic precipitators: use static charge to capture particulate contained in the exhaust gases. However, be aware that operational and safety problems associated with asphalt buildup on the collection grids have limited the use of this process.
- Incinerators and regenerative thermal oxidizers: combust the exhaust gases and destroy the liquid droplets, as well as the condensable and gaseous volatiles contained in the exhaust gases.
5.1.2 Work Practices
Reducing the concentration of asphalt fumes in the space above the hot asphalt also reduces the concentration of asphalt fumes emitted from the storage or processing tank through any openings (e.g., vents) that may be present. Asphalt is usually delivered to a plant by pipeline, truck, or rail. When pumping asphalt from the delivery vessel into the storage tank, receiving lines are attached to the storage tank below the liquid asphalt level (either by “bottom loading” or “submerged fill”). This practice helps reduce the emission of asphalt fumes during a loading operation.
The asphalt in the storage tanks is heated before its use in the manufacturing process. Excess heated asphalt is recirculated rather than returned to the storage tank to allow for lower storage temperatures of the asphalt. This procedure reduces the concentration of asphalt fumes emitted from the tank. Air sweeps* of storage tanks further reduce the concentration of asphalt fume in the space above the asphalt to a fraction of the LEL. Trumbore [1992] reported that recirculating excess asphalt in the tank(s) and using air sweeps lower asphalt fume concentrations in storage tanks by 50% to 75%. Current asphalt fume concentrations average less than 25% of the LEL in all storage tanks where these controls are used.
*Air sweeping is the practice of exhausting the vapor space above an asphalt storage tank rather than allowing the tank to vent through working and breathing losses only. This practice is very effective at lowering the vapor concentrations above the liquid to only a fraction of the lower explosive limit (LEL). The volume of air exhausted from the vapor space is typically 60 to 100 cfm. This exhaust stream is either filtered to remove condensable particulate or incinerated for volatile organic compounds (VOC) and particulate destruction.
5.2 Saturators
5.2.1 Engineering Controls
Complete enclosure, coupled with adequate exhaust ventilation is a commonly used engineering control for saturators. Typically, the enclosure includes not only the saturator but also the wet looper and, in some instances, the coater as well. Available fume-capture devices are the same as those discussed in Section 5.1.1 (mist eliminators, high-velocity air filters or fiberbed filters, electrostatic precipitators, and incinerators and regenerative thermal oxidizers).
In some plants, physical or operating constraints may make complete enclosure of the entire saturator-wet looper-coater series impractical. In these instances, canopy hoods with adequate local exhaust ventilation (LEV) can be used for the entire series of process units or for one process area such as the coater. Figure 5—1 depicts typical hood configuration.
5.2.2 Work Practices
The procedures for venting a totally enclosed coater are similar to those for saturators. For coaters with canopy hoods, the procedure for rethreading† a break in the line requires the operator to wear proper PPE including a respirator (see Appendix A) when needed. The exhaust fans should remain in operation during the rethreading process.
†Rethreading occurs at startup and following a line break. Whether at startup or following a line break, the process is similar. Line operators pull/feed the web (paper or fiber glass) through the machines and rolls on the line. All machines are stopped or slowed by a jog position during this process. If the rethreading process requires operators to feed the web through the saturator or coater, standard PPE for exposure to hot asphalt is recommended, i.e., respirators, safety glasses, leather work gloves, long-sleeve shirt or leather/Kevlar forearm/upper arm sleeve.
Figure 5—1. Total enclosure of saturator, wet looper, and coater. (Source: EPA [1988].)
5.2.3 Equipment Substitution
Another option for plants using saturators with both spray and dip processes is to rely exclusively on the dip process. The reduction in asphalt fume exposures in plants using the dip process has not been evaluated or quantified, although dip-only saturators are likely to generate lower airborne concentrations of asphalt fumes. The strong trend in the industry away from spray-process saturators has been generated by the need to reduce fire, explosion, and burn hazards associated with the spray processes. The switch to dip-only saturators has also been influenced by a variety of other factors, including the age and remaining useful life of the existing equipment; the cost and incremental exposure-reduction benefits of a dip-only saturator; and the comparative costs and exposure-reduction benefits of other available control options, such as increased exhaust flow rates, improved door seals, reduced apertures in existing enclosures, and improved hood designs in existing LEV systems.
5.3 Modified Bitumen Impregnation Vats
The emission of asphalt fumes from modified bitumen impregnation vats is controlled primarily with canopy hoods and adequate LEV. In many instances, these hoods extend over the cooling vats as well as the impregnation area.
5.4 Coaters
The capture of asphalt fumes at the coater is best achieved using either (1) full enclosure of the coating process (together with the saturator and wet looper) or (2) canopy hoods. In either case, adequate exhaust ventilation capacity is necessary to achieve complete capture of the roofing asphalt fumes generated by the coater. In some cases, extending the hood or canopy over the granule application section (which basically follows the coater) may be necessary to capture fumes emitted by the hot web after it has left the coater area.
5.4.1 Full Enclosure
The removal of asphalt fumes by all of the inplant exhaust ventilation systems should be routed to capture devices before discharge to the outside air. Examples of these capture devices include
- mist eliminators,
- high velocity air filters or fiberbed filters,
- electrostatic precipitators, and
- incinerators and regenerative thermal oxidizers
Section 5.1 gives more complete descriptions of these capture devices [EPA 1988]. All of these exhaust streams should be vented to the outside atmosphere after passing through the capture device.
- Follow these practices to minimize asphalt fume exposure to workers outside the coater enclosure:
- Keep to a minimum the number and size of openings in the enclosure.
- Reduce the amount of time during which doors to the enclosure are open during normal production runs.
- Maintain proper exhaust capacity of the ventilation system at all times [ACGIH 1998].
- Keep the coater and saturator temperatures as low as manufacturing specifications and variables will tolerate.
Higher exhaust rates due to excessive openings can lower the capture efficiency of the ventilation systems. To minimize the potential for fume exposures, all doors should be sealed and remain closed during operation of the line. The size of the apertures where the sheet enters and leaves the saturator should be minimized to reduce the potential for exposure to fumes and to ensure inward air flow from the workplace by the negative pressure in the enclosure. Adequate makeup air to the plant facility is important to ensure optimal capture velocity of the exhaust ventilation systems.
Assuming that an adequate configuration for the enclosure and proper exhaust ventilation is in place, the greatest potential for asphalt fume exposure during the coating process is during maintenance and repair work on the coater. Exposures to asphalt fumes can occur when workers must enter the enclosure during the manufacturing operation to correct a break in the operation of the line (occurs primarily from breakage of the felt sheet). Workers may need to enter the enclosure up to three times in an 8-hr shift, and usually spend from 10 to 20 min correcting the problem. Follow these practices to ensure that fume exposure to the worker entering the enclosure is minimized:
- Open all doors and increase the exhaust ventilation flow rate to reduce asphalt fume concentrations before entry.
- Ensure adequate space inside the enclosure to allow safe threading of the felt sheet and related maintenance activities.
- Wear proper PPE, including a respirator, as needed.
The exhaust ventilation rate in the enclosure must be sufficiently high to exhaust the asphalt fumes from the entire enclosure in the event of a break in the felt. Maintaining negative pressure in the enclosure is essential to prevent leakage of asphalt fumes into the work areas and to minimize fume concentrations inside the enclosure during the rethreading process. For formal maintenance during shutdowns, the equipment should be cooled and drained so that the potential for asphalt fume exposure is minimal.
5.4.2 Canopy Hood
In some plants, operational or plant configuration (layout) constraints preclude enclosure as a control option for coaters. These constraints are more likely to be found in older facilities where congested initial design or subsequent manufacturing modifications have created space restrictions. Therefore, enclosures cannot be installed without restricting access to process equipment or normal line operation. In these instances, asphalt fumes generated during the coating process can be collected by a canopy hood with adequate LEV.
Typical canopy hood dimensions vary from 5 to 8 ft in width and normally exceed the mat width by 2 to 3 ft. The length in the machine direction is typically 6 to 14 ft. Exhaust ventilation flow rates from canopy hoods located above the coater range from 4,000 to 8,000 cubic feet per minute (cfm). The vertical distance from the felt line to the hood opening should be minimized for optimal capture of the fume. Enclosure of the sides perpendicular to mat flow varies by facility. Insets in the canopy hood to block internal area and increase capture velocity at the hood periphery have proved effective in increasing fume capture efficiency. Cross air currents in the work area should be minimized to prevent interference of fume capture at the canopy hood.
5.5 Surfacing and Subsequent Processes
After the saturation and coating processes, the asphalt is no longer heated and asphalt fume generation decreases as the product cools. Typically, some release of asphalt fume occurs as the impregnated felt leaves the coater area; however, the felt sheet is immediately covered by a layer of granules and mineral-parting agents. The deposit of this mineral coating onto the felt sheet helps in the cool down process of the asphalt and decreases the release of asphalt fume.
The application of the mineral-parting agents generates the release of inorganic mineral dust. The dust contributes to the airborne concentration of particulates in the mineral application and cooling process areas of the plant. Local exhaust ventilation is generally installed at granule applicators, slate drums, dust drums, backdust applicators, and transfer rolls to reduce dust exposure. The amount of asphalt fume captured is probably determined by the proximity of the local exhaust ventilation system to where mineral granules are applied to the asphalt on the felt sheet. Owens Corning [1993a,b] reported that VOC emissions from the cooling section of the process are greatly reduced when there is effective dust collection before cooling. All manufacturers use local dust collection with capture in a bag-type dust collector. Dust collection flow rates vary significantly because of differences in plant configurations, and range up to 30,000 cfm.
Some general dilution ventilation occurs in the manufacturing buildings as a result of additional air being exhausted from the cooling sections of the manufacturing line. Although general ventilation of the manufacturing buildings varies widely in roofing manufacturing, it contributes to reducing exposures to asphalt fume. The types of ventilation systems used range from gravity ventilators, which provide makeup air to the process, to power ventilators, which exhaust large air volumes from the process building.
After the cooling process, the temperature of the product is lowered to near ambient temperatures and asphalt fume generation is minimal. Asphalt fume exposures may occur during the application of both sealant asphalt to shingle products and laminating asphalt to laminated shingle products [Owens Corning 1993a,b].
These low-mass asphalt applications are applied from “Star Wheel” applicators or by means of asphalt extruders. Local exhaust ventilation is installed at the point of asphalt application. Asphalt application temperatures are generally in the range of 250 to 400° F (120 to 205° C), but the sealant asphalt is cooled almost instantaneously by water, air, or soap solutions. Laminating asphalt is cooled by water baths or other means to eliminate product sticking. Because of the relatively small amounts of asphalt used in these processes and rapid cooling, fume generation is probably minimal; however, no data have been reported on the fume exposure that may occur during this process.
5.6 Work Practices and PPE
Good work practices and PPE should be used to prevent injury from combustion, explosion, or contact with hot asphalt. Before entering any enclosed area in a manufacturing plant, the area must be vented to remove asphalt fumes and ensure that adequate oxygen is available for workers. The equipment to be repaired must also be cooled to reduce the potential for burns. Maintenance work in potentially hazardous areas such as asphalt tanks, saturators, and coaters should be restricted to those personnel who are adequately trained and required to be in the area. Proper use of PPE including respirators (see Appendix A) should be mandatory. PPE that may be used during these operations includes the following:
- Safety glasses
- Face shields
- Long-sleeve shirts
- Respirators
- Coveralls or body suits
- Gloves
- Safety shoes
Appropriate PPE will reduce both dermal and inhalation exposures to asphalt fumes.
Effective work practices play an important role in preventing asphalt fume exposures and reducing the risks of acute and chronic health effects. For example, all operational instruments and fume control equipment must be properly maintained to ensure that they are effective in reducing asphalt fume exposures. Where respiratory protection is provided, all applicable OSHA requirements should be followed in accordance with a written respirator program, including use of NIOSH-approved respirators, training, fit-testing, and medical approval, as well as proper inspection, cleaning, maintenance, repair, and storage of respirators [29 CFR 1910.134].
Research Needs
The following research is suggested to reduce the risk of adverse health effects from occupational exposure to asphalt fumes during the manufacture of asphalt roofing products.
- Research should be conducted to characterize worker exposure to asphalt fumes in this segment of the industry.
- Short-term peak exposures should be identified as well as work shift TWA exposures.
- Studies should be conducted to deter-mine the effectiveness of current engineering controls in reducing worker exposure to asphalt fumes.
References
ACGIH [1998]. Industrial ventilation, a manual of recommended practices. 23rd ed. Cincinnati, OH: American Conference of Governmental Industrial Hygienists.
ACGIH [1999]. 1999 TLVs® and BEIs®. Threshold limit values for chemical substances and physical agents, biological exposure indices. Cincinnati, OH: American Conference of Governmental Industrial Hygienists.
AI [1990a]. Report to OSHA and NIOSH: status of Asphalt Industry Steering Committee research program on the health effects of asphalt fumes and recommendation for a worker health standard. Lexington, KY: Asphalt Institute.
AI [1990b]. Introduction to asphalt. 8th ed. Lexington, KY: Asphalt Institute, Manual Series No. 5 (MS-5).
AI [1991]. Final report: asphalt industry cross sectional exposure assessment study. Text and Appendix A. College Park, MD: Asphalt Institute.
Almaguer D, Miller AK, Hanley KW [1996]. Hazard evaluation and technical assistance report: Martin Paving Company, Yeehaw Junction, FL. Cincinnati, OH: U.S. Department of Health and Human Services, Public Health Service, Centers for Disease Control and Prevention, National Institute for Occupational Safety and Health, NIOSH HETA Report No. 95–0118–2565.
Apol AG, Okawa MT [1977]. Hazard evaluation and technical assistance report: Certain-Teed Products, Inc., Tacoma, WA. Cincinnati, OH: U.S. Department of Health, Education, and Welfare, Public Health Service, Center for Disease Control, National Institute for Occupational Safety and Health, NIOSH HHE Report No. 76–55–443, NTIS No. PB–81–143– 984/A02.
Apol AG, Okawa MT [1978]. Hazard evaluation and technical assistance report: Herbert Malarky Roofing Co., Portland, OR. Cincinnati, OH: U.S. Department of Health, Education, and Welfare, Public Health Service, Center for Disease Control, National Institute for Occupational Safety and Health, NIOSH HHE Report No. 76–56–458, NTIS No. PB–82–193–996/A02.
ARMA [1997]. Residential asphalt roofing manual. Calverton, MD: Asphalt Roofing Manufacturers Association.
ARMA [1999]. 1998 ARMA accident prevention contest report. Press release, March 17. Calverton, MD: Asphalt Roofing Manufacturers Association.
ASTM [1995]. 1995 Annual book of ASTM standards. Standard specification for asphalt used in roofing. Designation D312–95a. West Conshohockn, PA: American Society for Testing and Materials, pp. 49–50.
CFR. Code of Federal regulations. Washington, DC: U.S. Government Printing Office, Office of the Federal Register.
EPA [1988]. Review of new source performance standards for asphalt processing and asphalt roofing manufacture. Preliminary draft. Research Triangle Park, NC: U.S. Environmental Protection Agency, Office of Air and Radiation, Office of Air Quality Planning and Standards.
Exxon [1997]. Shift study of pulmonary function and symptoms in workers exposed to asphalt fumes. Final report submitted to Asphalt Industry Oversight Committee. East Millstone, NJ: Exxon Biomedical Sciences, Inc., Report No. 97TP31.
Fayerweather WE [1998]. Memorandum of January 5, 1998, from W.E. Fayerweather, Corporate Epidemiologist, Health Sciences, Owens Corning, to J.A. Wess, Education and Information Division, National Institute for Occupational Safety and Health, Centers for Disease Control and Prevention, Public Health Service, U.S. Department of Health and Human Services.
54 Fed. Reg. 2679 [1989]. Occupational Safety and Health Administration: air contaminants, final rule. Washington, DC: U.S. Government Printing Office, Office of the Federal Register.
57 Fed. Reg. 26182 [1992]. Occupational Safety and Health Administration: proposed rules. Washington, DC: U.S. Government Printing Office, Office of the Federal Register.
Freese and Nichols, Inc. [1994]. Specifications SW–1695 for Roswell Airport traffic control tower, Roswell Industrial Air Center. Department of Transportation, Federal Aviation Administration, Southwest Region. Fort Worth, TX: Freese and Nichols, Inc., Consulting Engineers.
Goppel JM, Knotnerus J [1995]. Fundamentals of bitumen blowing. In: Proceedings of the Fourth World Petroleum Congress, Section III/G, Paper 2, pp. 399–413.
Hanley KW, Miller AK [1996a]. Hazard eval-uation and technical assistance report: Spartan Paving Company, Lansing, MI. Cincinnati, OH: U.S. Department of Health and Human Serv-ices, Public Health Service, Centers for Disease Control and Prevention, National Institute for Occupational Safety and Health, NIOSH HETA Report No. 94–0365–2563.
Hanley KW, Miller AK [1996b]. Hazard eval-uation and technical assistance report: Granite Construction Company, Sacramento, CA. Cincinnati, OH: U.S. Department of Health and Human Services, Public Health Service, Centers for Disease Control and Prevention, National Institute for Occupational Safety and Health, NIOSH HETA Report No. 94–0408–2564.
Hicks JB [1995]. Asphalt industry cross-sectional exposure assessment study. Applied Occup Environ Hyg 10(10):840–848.
IARC [1985]. IARC Monographs on the evaluation of the carcinogenic risk of chemicals to humans: polynuclear aromatic compounds: Part 4: bitumens, coal tars and derived products, shale-oils and soots. Vol. 35. Lyon, France: International Agency for Research on Cancer.
Keating J, Vermilion D [1995]. Performance coating asphalt: a survey of the roofing plants in 1995. Granville, OH: Owens Corning Science and Technology, Owens Corning Memo Report 95–M–53, September 13.
King RW, Puzinauskas VP, Holdsworth CE [1984]. Asphalt composition and health effects: a critical review. Washington DC: American Petroleum Institute.
Kinnes GM, Miller AK, Burr GA [1996]. Hazard evaluation and technical assistance report: the Sim J. Harris Company, San Diego, CA. Cincinnati, OH: U.S. Department of Health and Human Services, Public Health Service, Centers for Disease Control and Prevention, National Institute for Occupational Safety and Health, NIOSH HETA Report No. 96–0130–2619.
Miller AK, Burr GA [1996a]. Hazard evaluation and technical assistance report: Koester Equipment Company, Evansville, IN. Cincinnati, OH: U.S. Department of Health and Human Services, Public Health Service, Centers for Disease Control and Prevention, National Institute for Occupational Safety and Health, NIOSH HETA Report No. 95–0307–2602.
Miller AK, Burr GA [1996b]. Hazard evaluation and technical assistance report: Staker Construc-tion Company, Casa Grande, AZ. Cincinnati, OH: U.S. Department of Health and Human Services, Public Health Service, Centers for Disease Control, National Institute for Occupa-tional Safety and Health, NIOSH HETA Report No. 96–0072–2603.
Miller AK, Burr GA [1998]. Hazard evaluation and technical assistance report: Bardon-Trimount, Stoughton, MA. Cincinnati, OH: U.S. Depart-ment of Health and Human Services, Public Health Service, Centers for Disease Control and Prevention, National Institute for Occupational Safety and Health, NIOSH HETA Report No. 97–0232–2674.
Niemeier RW, Thayer PS, Menzies KT, Von Thuna P, Moss CE, Burg J [1988]. A comparison of the skin carcinogenicity of condensed roofing asphalt and coal tar pitch fumes. In: Cooke M, Dennis AJ, eds. Polynuclear aromatic hydrocarbons: a decade of progress. Tenth International Symposium on Polynuclear Aromatic Hydrocarbons. Columbus, OH: Battelle Press, pp. 609–647.
NIOSH [1977]. Criteria for a recommended standard: occupational exposure to asphalt fumes. Cincinnati, OH: U.S. Department of Health, Ed-ucation, and Welfare, Public Health Service, Center for Disease Control, National Institute for Occupational Safety and Health, DHEW (NIOSH) Publication No. 78–106, NTIS Publication No. PB–277–333.
NIOSH [1987a]. NIOSH guide to industrial respiratory protection. Cincinnati, OH: U.S. Department of Health and Human Services, Public Health Service, Centers for Disease Control, National Institute for Occupational Safety and Health, DHHS (NIOSH) Publication No. 87–116.
NIOSH [1987b]. NIOSH respirator decision logic. Cincinnati, OH: U.S. Department of Health and Human Services, Public Health Service, Centers for Disease Control, National Institute for Occupational Safety and Health, DHHS (NIOSH) Publication No. 87–108.
NIOSH [1988]. NIOSH testimony on the Occu-pational Safety and Health Administration’s proposed rule on air contaminants, August 1, 1988. NTIS No. PB–91–115–337.
NIOSH [1996]. NIOSH guide to the selection and use of particulate respirators certified under 42 CFR 84. Cincinnati, OH: U.S. Department of Health and Human Services, Public Health Service, Centers for Disease Control and Prevention, National Institute for Occupational Safety and Health, DHHS (NIOSH) Publication No. 96–101.
NIOSH [in preparation]. NIOSH hazard review: health effects of occupational exposure to asphalt. Cincinnati, OH: U.S. Department of Health and Human Services, Public Health Service, Centers for Disease Control and Prevention, National Institute for Occupational Safety and Health.
Norseth T, Waage J, Dale I [1991]. Acute effects and exposure to organic compounds in road maintenance workers exposed to asphalt. Am J Ind Med 20:737–744.
NRCA [1995]. 1995–1996 Annual market survey. Rosemont IL: National Roofing Contractors Association.
NRCA [1996]. NRCA Roofing and water-proofing manual. 4th ed. Rosemont IL: National Roofing Contractors Association.
Okawa MT, Apol AG [1977]. Hazard evaluation and technical assistance report: Certain-Teed Products, Inc., Richmond, CA. Cincinnati, OH: U.S. Department of Health, Education, and Welfare, Public Health Service, Center for Disease Control, National Institute for Occupational Safety and Health, NIOSH HHE Report No. 76–54–436, NTIS Publication No. 89–140–198.
Okawa MT, Apol AG [1978a]. Hazard evaluation and technical assistance report: Johns-Manville Products Corporation, Vernon, CA. Cincinnati, OH: U.S. Department of Health, Education, and Welfare, Public Health Service, Center for Disease Control, National Institute for Occupational Safety and Health, NIOSH HHE Report No. 77–57–460, NTIS No. PB–82–197–435/A02.
Okawa MT, Apol AG [1978b]. Hazard evalu-ation and technical assistance report: Johns-Manville Products Corporation, Pittsburg, CA. Cincinnati, OH: U.S. Department of Health, Education, and Welfare, Public Health Service, Center for Disease Control, National Institute for Occupational Safety and Health, NIOSH HHE Report No. 77–56–467, NTIS No. PB–291–657/A02.
Owens Corning [1993a, unpublished]. Internal document: Owens/Corning Fiberglas Environmental Affairs, air emission sampling data. Granville, OH: Owens Corning Science and Technology.
Owens Corning [1993b, unpublished]. Internal document: Owens/Corning Fiberglas Environmental Services, roofing plant process data. Granville, OH: Owens Corning Science and Technology.
Pozzoli L, Cottica D, Maugeri U, Clonfero E [1985]. PAH in air and in biological fluids: experimental surveys to establish the TLV. Ann Am Conf Ind Hyg 12:317–320.
Roberts FL, Kandhal PS, Brown ER, Lee D-Y, Kennedy TW [1996]. Hot mix asphalt materials, mixture design and construction, 2nd ed. Lanham, MD: NAPA Research and Education Foundation.
Sax NI, Lewis RJ [1987]. Hawley’s condensed chemical dictionary. 11th ed. New York: Van Nostrand Reinhold Co.
Shell [1995]. The Shell bitumen industrial handbook. Surrey, UK: Shell Bitumen, Riversdell House.
Sivak A, Menzies K, Beltis K, Worthington J, Ross A, Latta R [1989]. Assessment of the cocarcinogenic/promoting activity of asphalt fumes. Cincinnati, OH: U.S. Department of Health and Human Services, Public Health Service, Centers for Disease Control, National Institute for Occupational Safety and Health, NIOSH No. 200–83–2612, NTIS Publication No. PB–91–110–213.
Sivak A, Niemeier R, Lynch D, Beltis K, Simon S, Salomon R, Latta R, Belinky B, Menzies K, Lunsford A, Cooper C, Ross A, Bruner R [1997]. Skin carcinogenicity of condensed asphalt roof-ing fumes and their fractions following dermal applications to mice. Cancer Lett 117:113–123.
Speight JG [1992]. Asphalt. In: Kroschwitz JI, Howe-Grant M, eds. Kirk-Othmer encyclopedia of chemical technology. 4th ed. Vol. 3. New York: John Wiley & Sons, Inc., pp. 689–724.
Trumbore DC [1992]. Asphalt tank explosion hazards: appendix for report 92–T–56. Granville, OH: Owens Corning Science and Technology, Owens Corning Memo Report 92–T–57, August 17.
Trumbore DC, Wolever RD, Vermilion DR [1992]. Air blowing of asphalt and drop-back: Part I. Granville, OH: Owens Corning Science and Technology, Owens Corning Memo Report 92–T–53, February 10.
Vo-Dinh T [1989]. Significance of chemical analysis of polycyclic aromatic compounds and related biological systems. In: Vo-Dinh T, ed. Chemical analysis of polycyclic aromatic compounds. A series of monographs on analytical chemistry and its applications. Vol. 101. New York: John Wiley & Sons, Inc., pp. 1–5.
Appendix Respirators
At most worksites where hot asphalt or asphalt-based paints are used, concentrations of asphalt fume or aerosol are generally below the NIOSH REL of 5 mg/m3. However, constantly changing environmental and worksite conditions may result in fluctuating airborne concentrations of asphalt fumes and asphalt-based paint aerosols. Such fluctuations may result in ex-posures exceeding the NIOSH REL and warrant the use of respiratory protection. If respirators are required at the worksite, the employer is responsible for ensuring that respirators are NIOSH-approved and that all OSHA regulations pertaining to the implementation of a respirator program are followed. Important elements of these OSHA regulations include the following [29 CFR 1910.134]:
- An evaluation or the worker’s ability to perform the work while wearing a respirator
- Regular training of workers
- Periodic environmental monitoring
- Respirator fit-testing, maintenance, inspection, cleaning, and storage
- Periodic changing of cartridges
- Cartridge testing for service life
No NIOSH-approved respirator filter cartridge or canister exists specifically for asphalt fumes or aerosols. But the respirators listed below may reduce exposures:
- Any half-facepiece, air-purifying respirator equipped with a combination R100 or P100 filter and an OV (organic vapor) cartridge, or
- Any powered air-purifying respirator (PAPR) with a hood, helmet, or loose-fitting facepiece equipped with a combination HEPA filter and OV cartridge.
Note: The appropriate respirator filters are R100, P100, or HEPA as listed under 42 CFR 84 [NIOSH 1996]. The appropriate OV cartridge or canister should contain a charcoal sorbent. This type of protection may also be used when the potential exists for exposure to dusts containing coal tar or asbestos.
A comprehensive assessment of workplace exposures should always be performed to en-sure that the proper respiratory protection is used. Other types of respirators can provide a higher level of protection and may be required under certain conditions (e.g., work in con-fined spaces) [NIOSH 1987a,b].